Researchers at ANEMEL have achieved a significant advancement in the field of water splitting by developing a highly efficient and stable catalyst for water electrolysis, one that does not rely on the scarce and expensive platinum group metals (PGMs). This breakthrough, published in the journal Energy & Environmental Science, paves the way for more sustainable and cost-effective hydrogen production, a key step toward the green hydrogen revolution.
The Challenge with Current Water Electrolyzers
At the core of the current generation of anion exchange membrane (AEM) electrolyzers lies a critical challenge: reliance on PGMs, particularly platinum and iridium, which serve as catalysts in the cathode of the electrolyzer. These metals are not only rare and expensive but also make up a significant portion of the overall cost of electrolyzers. Moreover, the limited availability of PGMs poses a major barrier to the large-scale deployment of electrolyzers for green hydrogen production. Green hydrogen, produced using renewable energy through water electrolysis, is considered one of the most promising solutions to the energy transition, offering a sustainable alternative to fossil fuels in industries like transportation and manufacturing.
To reduce the cost and environmental impact of water electrolysis, researchers have been searching for alternatives to PGMs, aiming to develop more abundant and cheaper materials that can still match the performance and stability of their platinum-based counterparts.
ANEMEL’s Breakthrough: A PGM-Free Catalyst for Water Electrolysis
The researchers at ANEMEL, in collaboration with École Polytechnique Fédérale de Lausanne (EPFL) in Switzerland, have developed a PGM-free catalyst that can efficiently perform the crucial reaction at the cathode where hydrogen is produced. This new catalyst is composed of nickel and molybdenum, both of which are abundant and relatively inexpensive metals compared to platinum. By eliminating PGMs from the equation, the researchers have significantly lowered the cost of the catalyst, making it more feasible for widespread use in hydrogen production.
The study marks an important milestone in making AEM electrolyzers more accessible and affordable. Not only does this work decrease reliance on rare metals, but it also helps to improve the recyclability of electrolyzer components, thereby reducing waste and promoting a more sustainable energy ecosystem.
The Importance of Electrodeposition and Self-Supported Catalysts
To achieve this breakthrough, the ANEMEL team turned to an innovative method of catalyst fabrication: electrodeposition. Electrodeposition is a technique commonly used to coat surfaces with a metal layer, utilizing electrolysis to drive the chemical deposition of ions from a solution. In this case, the team used electrodeposition to grow the catalyst directly onto the gas diffusion layer (GDL), which serves as the support for the catalyst. This GDL allows gases to diffuse while providing a conductive pathway for the current.
Self-supported catalysts are those that are directly formed on the support structure, eliminating the need for separate catalyst substrates. This approach is beneficial because it enhances the overall stability and performance of the catalyst, while also simplifying the manufacturing process. The GDL is made of materials such as carbon paper, nickel foam, and nickel felt, each of which plays a role in enabling efficient gas diffusion and electrical conductivity.
The Role of Nickel and Molybdenum in the Catalyst
The key to this breakthrough lies in the combination of nickel and molybdenum. Both metals are not only abundant and affordable, but also have favorable electrochemical properties. While nickel has long been recognized as a promising candidate for water splitting, molybdenum offers excellent catalytic properties for the hydrogen evolution reaction (HER), the critical reaction in electrolysis that produces hydrogen.
The researchers’ innovation was in optimizing the electrodeposition bath and adjusting the deposition conditions, including the use of high-current density. This allowed for the creation of a compact and thick catalyst structure that performs well under the high-current conditions typical of electrolyzer environments.
Key Advances in Electrodeposition Technique
The ANEMEL team’s method for growing this PGM-free catalyst involved some novel decisions regarding the electrodeposition bath. Unlike most common techniques, which use boric acid as a buffering agent to stabilize the pH of the solution, the researchers chose to forgo such stabilizers. Instead, they relied on an electrolyte with high conductivity, which allowed them to use a higher deposition current density. This high conductivity was crucial in enabling the growth of a more compact and stable catalyst, which is essential for high-performance water splitting.
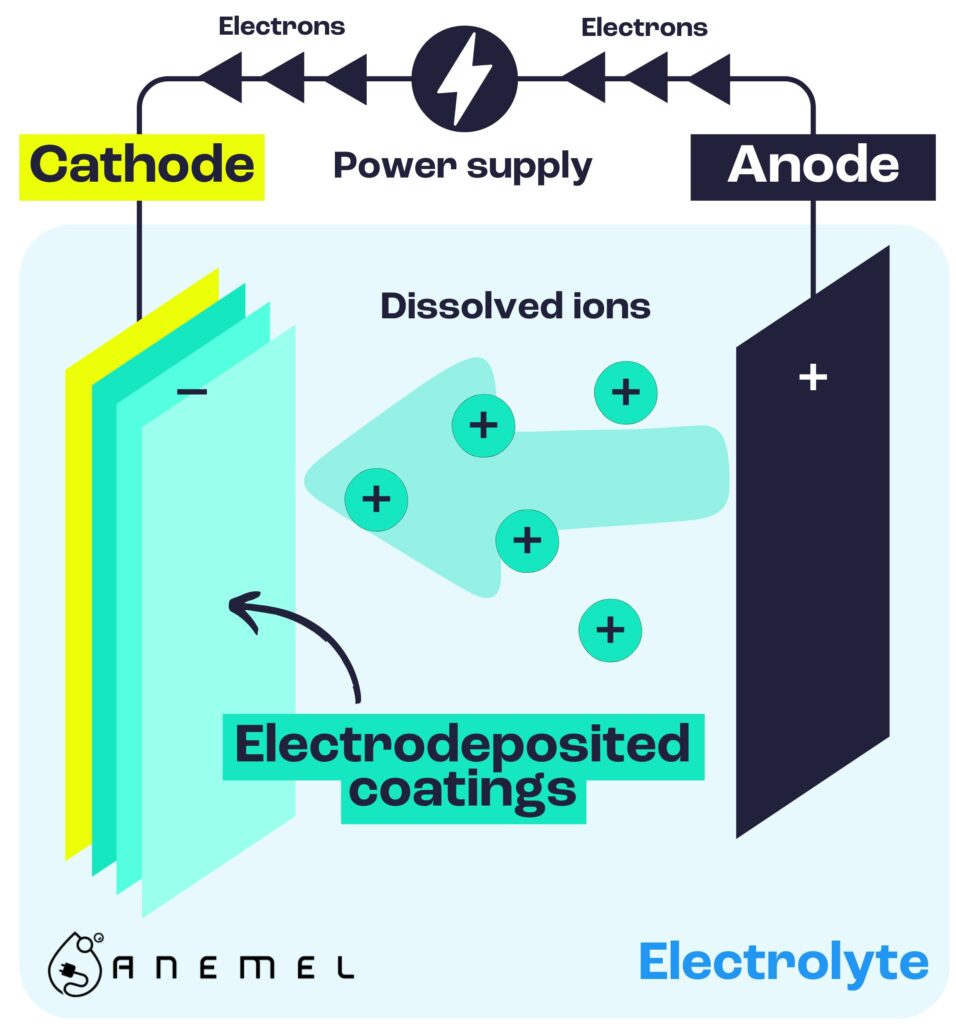
As Ariana Serban, the doctoral researcher leading the study, explains, “The high conductivity in the electrolyte was critical as it affected the electrodeposition process, enabling us to grow a more robust catalyst that could withstand the high stress of operation in electrolyzers.”
Achieving High Performance and Stability
The resulting catalyst achieved impressive performance metrics, even at high current densities of up to 3 A/cm², which is a crucial threshold for electrolyzers operating in real-world conditions. High current densities are important because they simulate the stress that electrolyzers will experience during rapid, large-scale hydrogen production. The ability to perform at such high current densities indicates that the catalyst is both highly active and stable under the operating conditions typically found in industrial applications.
In fact, the performance of the ANEMEL catalyst rivals that of benchmark platinum catalysts, and in some cases, it even outperforms them in terms of stability. This is a remarkable achievement, as PGM-free catalysts have historically struggled to match the performance of platinum in terms of longevity and resistance to degradation.
Serban and her team believe their catalyst ranks among the top 100, or even top 50, non-PGM catalysts in terms of performance, signaling that this development represents a significant step forward in the search for cost-effective hydrogen production solutions.
Catalyst Characterization and Structural Insights
In addition to the impressive performance, the team also conducted detailed characterization of the catalyst to understand its behavior during the water-splitting reaction. One of the key findings was that the molybdenum atoms in the catalyst underwent a structural transformation during operation. These atoms migrated to the surface of the catalyst, driven by distortions in the bulk material, a phenomenon that helped improve the catalyst’s performance.
Some of the molybdenum atoms became oxidized, losing electrons in the process. These oxidized species played a key role in the water-splitting reaction, contributing to the overall hydrogen production. This structural change is believed to be an important factor in the catalyst’s outstanding performance, as it demonstrates how materials can be optimized to perform better than their individual components would suggest.
Implications for Green Hydrogen Production
The development of this PGM-free catalyst is an important milestone in the quest for large-scale green hydrogen production. Green hydrogen, produced using renewable energy sources through water electrolysis, is seen as a clean alternative to hydrogen produced from fossil fuels. It can be used to decarbonize sectors that are hard to electrify, such as heavy industry, transportation, and energy storage.
By developing a stable, efficient, and cost-effective catalyst for water electrolysis, ANEMEL’s work brings us one step closer to realizing the potential of green hydrogen as a major player in the global energy transition. This advancement not only helps to reduce the cost of electrolyzers but also makes it possible to produce hydrogen at a much larger scale without relying on rare and expensive materials.
Conclusion
The PGM-free catalyst developed by the ANEMEL research team represents a game-changing breakthrough for hydrogen production and electrolysis. By eliminating the need for platinum group metals, the researchers have created a catalyst that is both affordable and highly efficient, positioning it as a potential game-changer in the production of green hydrogen.
This work highlights the power of innovative materials and electrodeposition techniques in overcoming the challenges faced by the renewable energy sector. It also brings us one step closer to a future in which sustainable hydrogen plays a central role in decarbonizing global industries, helping to tackle the climate crisis and usher in a new era of clean energy.
Reference: Ariana Serban et al, An oxide-promoted, self-supported Ni4Mo catalyst for high current density anion exchange membrane water electrolysis, Energy & Environmental Science (2024). DOI: 10.1039/D4EE04528A